How to prolong the working life of a pellet machine?
Every machine has a certain working life. It depends on the wearing parts. In terms of pellet machines, the wearing parts includes roller, die (ring die or flat die), bearing, and gearbox, etc. the working life of a ring die is 800-1200 hours, a flat die is 600-800 hours, and a roller is around 1000 hours. The working life is determined by the product quality, but also influenced by your using habits. Proper use and regular maintenance can prolong the working life of a pellet machine.
Feed the pellet machine with oil mixture
Every time when you finish pellet production, feed oil mixtures (mixed sawdust and used oil) to the pellet machine and let it operate for 1-2 minutes, then you can shut down the machine. After this process, the die holes are filled with oil mixture and won't get blocked by the raw materials. With this step, you can start making pellets directly the next time. It can not only save your time but also prolong the working life of the pellet machine.
But if you don’t use the pellet machine for over 1 month, you’d better take out the oil mixture in the die, or they would get hardened and not easy to clear up. This is not good for later use.
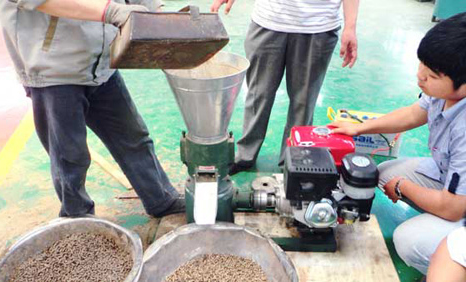
Control the purity of raw materials
Before starting the machine, make sure there is no foreign matters in the feed hopper. But don’t put you hand into the hopper when the pellet machine is running. If there is abnormal noise in the feed hopper, you should shut down the machine and remove the foreign matters, and start it again.
Make sure there is no stones, metals, large wood blocks in the raw materials. Condition permitting, install a Tublar Magnet or a RCYB on the feed hopper to prevent metals getting into the pellet machine. Besides, you can use a automatic feeder to achieve uniform feeding, so that the pellet production is more smooth.
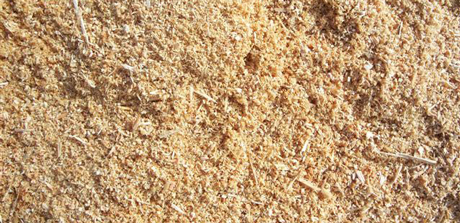
Control the moisture content
Usually, the moisture content of raw materials should be 10%-18%. If the moisture content is too low, the raw materials will be too hard. They will increase the power consumption and the abrasion of the pellet machine. On the other hand, raw materials with high moisture content are hard to pulverize, which will increase the abrasion of the hammer mill. Besides, The pressing and friction in the pellet mill will heat up the raw materials and cause the moisture to evaporate. The evaporated moisture will mix with the wood powders and block the holes on the die, thus reducing the pellet production.
Clean the components regularly
The pelletizing process will generate a lot wood dust, but the pellet machine are usually not equipped with dust protection device. This requires us to clean the roller, die, main shaft and bearing regularly. Clear up the sawdust in slots, gaps and screw holes, or they may cause fracture of the components.
If you don't use the pellet machine for long time, I recommend you to dispatch the components and clear up the pellets inside the die and the sawdust attached to the mold surface, incase they become stiff and hard to remove. Meanwhile, the sawdust will absorb water and accelerate the corrosion of the components.
Lubricate the roller, shafts and gearbox
Before the first time use, add lubricate oil to the gearbox, shafts and bearings. In daily use, you should lubricate the roller and main shaft every day, and lubricate the gearbox every a half year. If the roller is short of oil, it will cause damage to the bearing and roller shaft, even break down the pellet machine.
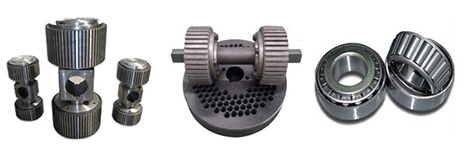
Choose suitable size of die
The hole size of the die is from 2.5-10mm, and the 4mm, 6mm and 8mm is the most popular. The size of die is determined by the raw materials. If the holes are undersized, the pellet yield will be low and even no pellets coming out. Meanwhile, they will increase the pressure between the roller and die and shorten the working life of the pellet machine. So you need to consult the sales to choose a suitable die.
Adjust the clearance between the roller and die
The roller and die (flat die or ring die) is the core part of the pellet machine. Their clearance influence the pelletizing effect and the working life. The suitable clearance is between 0.1mm and 0.3mm. If the clearance is larger than 0.3mm, the raw material layer will be too thick and reduce the pellet yield. If the clearance is less than 0.1mm, the abrasion of the roller and die will increase, and influence the working life.
In flat die pellet machine, there are adjusting nuts on the 2 sides of the machine body. Tighten them up and screw back for 15°-30°. Keep the two bolts in balanced positions. Then, you can fasten the lock bolts. In ring die pellet machine, make sure the clearance between each side of the roller and the ring die is the same. In other words, the roller and ring die should in the same axis, in case the eccentric roller cause abrasion to the ring die.
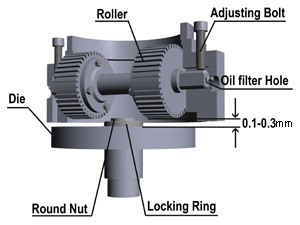
Place the pellet machine in dry places
To protect the pellet machine from damp, we need to place the pellet machine in a clean, dry and ventilated environment. The metal parts are easy to get rust under moist condition, and the electric motor will have shortcut or electric leakage. These will shorten the working life of the pellet machine.
We receive enquiries in English, Español (Spanish), Русский язык (Russian), Français (French) and العربية (Arabic). Our professional team will reply to you within one business day. Please feel free to contact us!